Products
Product description
Product introduction
Catalytic combustion equipment, also known as catalytic combustion exhaust gas treatment equipment, catalytic exhaust gas treatment equipment, regenerative catalytic combustion equipment, is a catalyst that rapidly oxidizes hydrocarbons in organic waste gas to water under low temperature conditions. Carbon dioxide, for the purpose of governance. The catalytic combustion process is carried out in a catalytic converter for the combustion of organic waste gas. The organic waste gas is preheated to 200 to 400 C through a heat exchanger, and then enters the combustion chamber. When passing through the catalyst bed, the molecules of the hydrocarbon and the oxygen molecules in the mixed gas are respectively adsorbed on the surface of the catalyst to be activated. Since surface adsorption reduces the activation energy of the reaction, hydrocarbons and oxygen molecules are rapidly oxidized at lower temperatures to produce carbon dioxide and water.
Exhaust emission component
VOCsIngredients: xylene, toluene, butyl acetate, etc.
Basic properties of exhaust gas components
Contaminant | Dissolved in water | Boiling point / ° C | Flash point / ° C | Lower explosion limit | Explosion on line |
---|---|---|---|---|---|
Toluene | Insoluble | 110.6 | 4.4 | 1.27% | 7.0% |
Xylene | Insoluble | 137-140 | 17.4 | 1.09% | 6.6% |
Ethyl acetate | 10% | 77.1 | 7.2 | 2.18% | 11.4% |
Catalytic combustion purification VOCs mechanism
Catalytic combustion is a typical gas-solid phase catalytic reaction, which is essentially the deep oxidation of active oxygen. In the catalytic combustion process, the catalyst acts to reduce the activation energy, and at the same time, the catalyst surface has an adsorption effect, so that the reactant molecules are concentrated on the surface to increase the reaction rate and accelerate the reaction. With the aid of the catalyst, the organic exhaust gas can be flamelessly burned at a lower light-off temperature, and oxidatively decomposed into CO, and H2O, while releasing a large amount of heat energy.
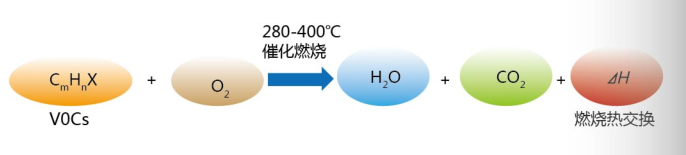
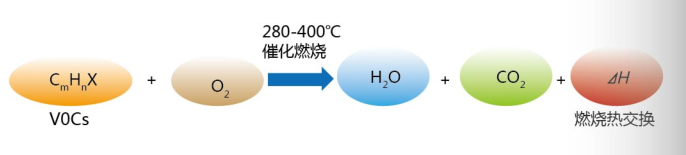
Catalytic combustion purification VOCs equipment structure module
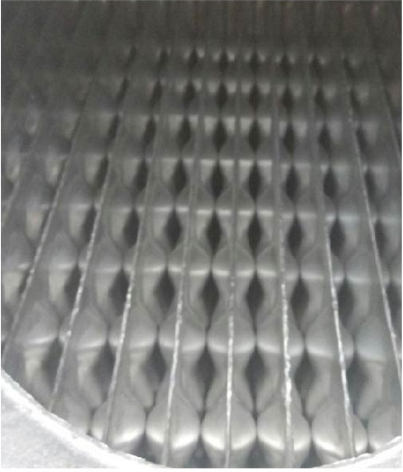
Plate heat exchanger
A plate heat exchanger is a high-efficiency heat exchanger in which a series of metal sheets having a constant corrugated shape are stacked. A thin rectangular channel is formed between the various sheets, and heat is exchanged through the sheets. Plate heat exchangers are ideal for heat exchange between liquid, liquid and liquid. The utility model has the advantages of high heat exchange efficiency, small heat loss, compact and light structure, small occupied area, wide application and long service life. In the case of the same pressure loss, the heat transfer coefficient is 3-5 times higher than that of the tube heat exchanger, and the floor space is one-third of the tube heat exchanger, and the heat recovery rate can be as high as 90% or more.
Heating chamber and catalyst
The heating chamber is heated by an integrated U-shaped heating tube. The heating method has the characteristics of no pollution, stable operation, more convenient, and rapid temperature rise. It is automatically controlled by the electronic control system. When the exhaust gas temperature is lower than a certain temperature (can be set), the heating is performed. The device automatically heats the exhaust gas. When the exhaust gas temperature is higher than a certain temperature (can be set), the burner is disconnected from the power supply to save energy and achieve safe operation.
Scope of application
Catalytic combustion is suitable for the treatment of high-concentration exhaust gas. If the concentration is not high, activated carbon adsorption equipment and photolysis equipment can be used. The system has high purification efficiency and high degree of automation, and is in a leading position in China. It is widely used in petroleum, chemical, rubber, paint, coating, printing and other industries, such as benzene, toluene, xylene, ethylbenzene and other benzene waste gas and ketones, alcohols, aldehydes, esters, anhydrides, Organic waste gases such as terpenoids, amines, cyclohexane, cyclohexene, cyclohexanone, methyl mercaptan, ethyl mercaptan, C mercaptan, and carbon disulfide can all be purified.
Product Features
The system has low operating cost, does not need to consume a large amount of electric energy or gas, and saves operating costs; ★ does not produce secondary pollutants such as nitrogen oxides (NOx); ★ low investment; ★ fully automatic control, ready to use; Impact load, not easily affected by pollutant concentration and temperature changes; ★ efficient heat recovery rate, heat recovery efficiency & ge; 95% and other advantages.