ENGLISH
Product description
Product Image
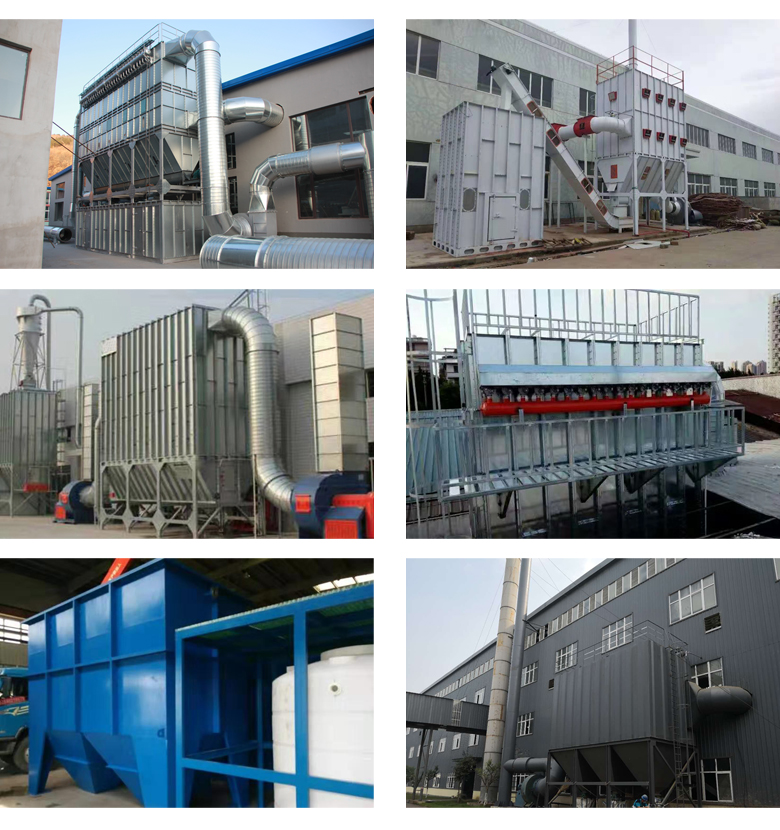
product description
The pulse-jet bag filter was invented by the American Reinhauer in the 1950s. It is a bag-type dust collector that periodically blows compressed air into the filter bag to remove the dust from the filter bag. High-efficiency dust collector, the purification efficiency can reach more than 98%, and the pressure loss is about 1200~1500Pa. The filter wear is light, the service life is long, the operation is stable and reliable, and it has been widely used. Deashing requires a pressure source for cleaning power and consumes a certain amount of energy.
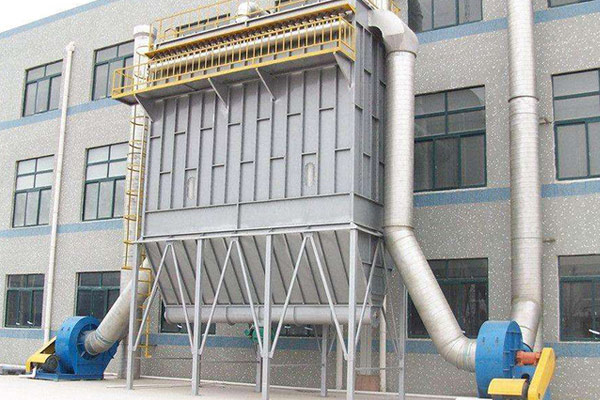
The dust-containing gas enters the ash hopper under the attraction of the induced draft fan, and is evenly distributed to each filter bag after passing through the deflector. The dust is intercepted on the outer surface of the filter bag, and the gas is passed through the filter bag and discharged through the clean room.
The dust bag trapping dust on the outer surface of the filter bag will reduce the permeability of the filter bag, so that the resistance of the dust collector will increase continuously, and the resistance will reach the set plant (differential pressure control) or the filter time will reach the setting. Value (time control), the normally-closed pulse valve is opened under the pulse injection control of the pulse injection controller PLC for a short period of time (about 0.1s). The high-pressure gas instantaneously enters the injection pipe from the air bag and is sprayed at high speed. Blow holes are ejected. The high velocity airflow into the filter bag also produces multiple secondary drainages of the injected gas. The combination of the jet flow and the secondary drainage causes the pressure inside the filter bag to rise rapidly, and the filter bag is changed from the original concave shape to the convex shape, and a large reverse acceleration is generated when the deformation amount reaches a maximum value. The dust adsorbed on the filter bag mainly falls off the surface of the filter bag under the action of the reverse acceleration, and falls into the ash hopper, and the resistance of the dust remover decreases accordingly. The process of removing dust from the surface of the filter bag is called cleaning. The cleaning work is carried out in a row. Each time the pulse valve is actuated, a row of filter bags is cleaned. The pulse valve operates in sequence at a set time interval and sequence until a cycle is completed. The entire dust collector completes a cleaning cycle.
Schematic
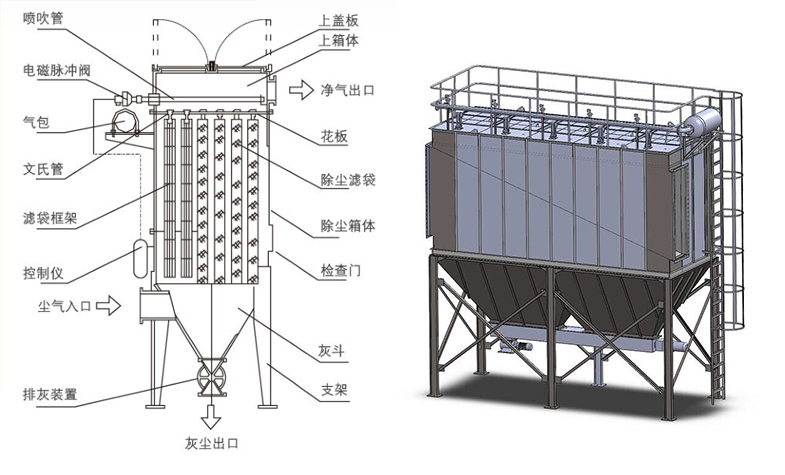
On-site process flow chart
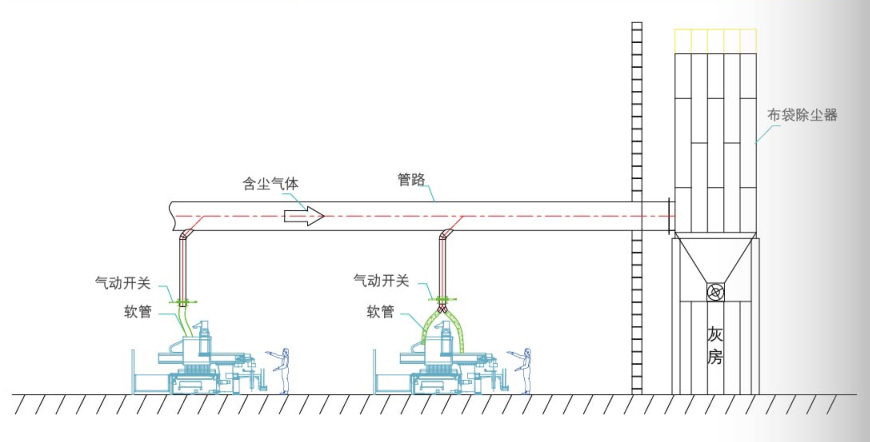
Bag process and cleaning state diagram
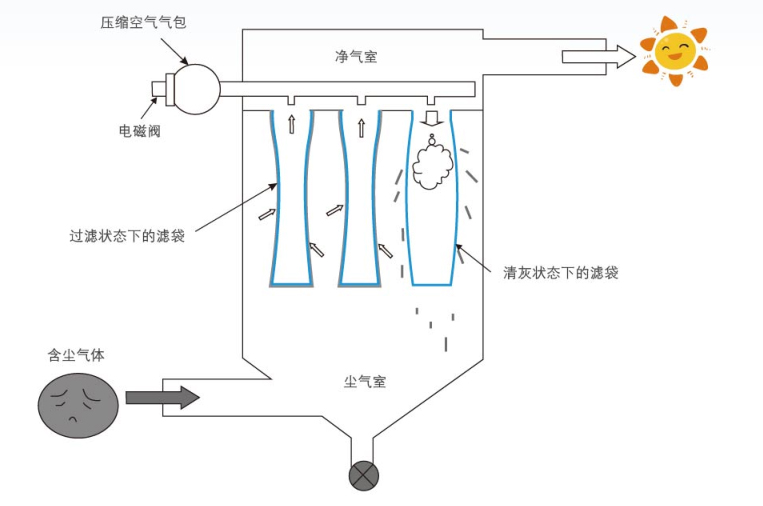
Features
Strong cleaning ability and high dust removal efficiency;
Low emission concentration and low air leakage rate;
Less energy consumption, less steel consumption, and less floor space;
Stable operation and good economic returns.
Scope of application
Performance parameter
Serial number | Model number | Air volume m3/h | Purification efficiency | Model representation meaning |
---|---|---|---|---|
1 | HFDM-30-Y | 5000-10000 | 98% | D:Low pressure injection |
2 | HFDM-60-Y | 10000-15000 | 98% | M:Cleaning method is pulse |
3 | HFDM-90-Y | 15000-20000 | 98% | 30:Total filtration area |
4 | HFDM-120-Y | 20000-25000 | 98% | Y:The filter bag is round |
5 | HFDM-150-Y | 25000-30000 | 98% |